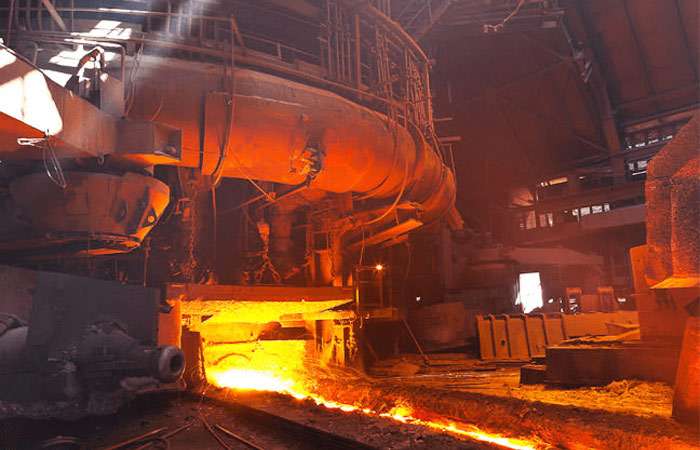
تحقیق درباره مراحل تولید آهن به زبان ساده
مجله بهترینها سرویس محتوای آموزشی – آهن یکی از مهمترین عناصر روی کره زمین است که بدون آن حیات مکانیزه مدرن تقریبا غیرممکن است. این فلز که عملا به شکل خالص وجود ندارد، یکی از پرکاربردترین عناصر در تمامی صنایع است. فولاد شاخه بزرگی از آلیاژهای آهن است که وابستگی انسان به آن غیرقابل انکار است. اما این عنصر حیاتی برای انسان چگونه استخراج می شود؟ مراحل تولید آهن و فرآیندهای مختلف آن چیست؟
آهن چیست؟
آهن با نماد Fe و عدد اتمی ۲۶، پس از آلومینیوم فراوان ترین عنصر روی کره زمین است. این فلز در گروه 8 و دوره 4 جدول تناوبی قرار دارد و نقطه ذوب آن نزدیک به 1538 درجه سانتیگراد است. آهن در محیط های آب و هوایی به راحتی اکسید می شود و به همین دلیل در بیشتر موارد به صورت اکسید (سنگ هماتیت Fe2O3) در طبیعت یافت می شود.
انسان حدود پنج هزار سال پیش آهن را کشف کرد. مصریان و جوامع بین النهرین جزو اولین تمدن هایی بودند که قادر به استخراج سنگ آهن بودند.
بیشتر بخوانید: تفاوت فولاد و چدن چیست و هر کدام چه ویژگی هایی دارند؟
مراحل مختلف تولید آهن و فرآیندهای آن
فرآیندهای تولید آهن و استخراج آن از سنگ آهن پیچیده و یک واحد دانشگاهی در رشته مهندسی مواد است. از این رو فقط به صورت مختصر به مراحل تولید آهن می پردازیم و به زبانی ساده بیان می کنیم.
سنگ ها عبارتند از: همانطور که اشاره کردیم آهن به صورت خالص در زمین یافت نمی شود و تمام عناصر استخراج شده از سنگ آهن است.
این سنگ ها دارای ترکیبات مختلفی هستند و فرآیند استخراج و تصفیه با توجه به نوع ترکیب انجام می شود. از جمله سنگ های معروف با ترکیب آهن می توان به موارد زیر اشاره کرد: هماتیت، مگنتیت، گوت، لیموناد و… اشاره کرد. تفاوت این سنگ ها به دلیل تعداد متفاوت اکسید آهن و ترکیب اکسیدهای مختلف است.
فرآیند تولید آهن در کوره های مخصوص ذوب آهن صورت می گیرد. به این ترتیب:
1. از بالای کوره بلند، سنگ آهن (سنگ آهن)، کک و سنگ آهک آورده می شود که به آن کوره بلند یا بار کوره نیز می گویند.
عملگرهای جریان دو کار انجام می دهند:
- ذوب ناخالصی ها در سنگ آهن که نقطه ذوب آن بالاتر از دمای معمولی کوره است.
- برخی از عناصری که همزمان با سنگ آهن تجدید می شوند در آهن حل می شوند یا با آهن ترکیب می شوند و قابل جدا شدن نیستند و مواد مذاب قبل از ترکیب شدن با آهن با این ناخالصی ها ترکیب می شوند. نوع جریان بستگی به ترکیب بار کوره دارد.
مواد جریان:
- اگر سنگ آهن آهکی (قلیایی) باشد، ماده مذاب باید اسیدی باشد (مثلاً SiO2 سیلیس).
- اگر سنگ آهن سیلیسی (اسیدی) باشد، شستشو باید قلیایی باشد (مانند سنگ آهک، دولومیت و سنگ های فسفات).
مراحل مختلف تولید آهن و فرآیندهای آن
2. جریان شدیدی از هوای گرم از ته فر می وزد. این هوای گرم گاهی با اکسیژن تقویت می شود. هوای ورودی با کک یا کربن ترکیب می شود و مقدار زیادی گرما آزاد می کند. در این مرحله دمای فر به بالاترین مقدار یعنی حدود 1500 درجه سانتیگراد می رسد.
توجه: برای به دست آوردن یک تن چدن حدود 5-6 تن هوا مورد نیاز است که از مخلوط دو گاز اکسیژن و نیتروژن به نسبت 1 به 4 تشکیل شده است. در کوره بلندهای جدید هوا به داخل کوره دمیده می شود. توسط کمپرسورهای توربین
3. دی اکسید کربن حاصل به آرامی افزایش می یابد و با کک ورودی واکنش می دهد و مونوکسید کربن تشکیل می دهد.
4. مونوکسید کربن اکسیژن را از اکسید آهن می گیرد و آهن را تشکیل می دهد و دی اکسید کربن به ته کوره جریان می یابد.
5. سنگ آهک به حذف ناخالصی ها کمک می کند، زیرا سنگ آهک با ناخالصی ها واکنش نشان می دهد و خاکستر یا سرباره تشکیل می دهد، که سیلیکات کلسیم است که در بالای آهن مذاب شناور است و از فلز در برابر اکسیداسیون توسط هوای به دام افتاده محافظت می کند پایین کوره
6. سرباره در فواصل منظم از کوره خارج می شود. سرباره اغلب در راه سازی استفاده می شود.
سرباره: این ماده مذابی است که در نتیجه برهمکنش بین ناخالصی های مواد مذاب، سنگ آهن، سوخت و اکسید موجود در فلز به وجود آمده است از آهن خام
اجزای اصلی سرباره عبارتند از: مژه های حسرت ، Al2O3 ، SiO2 ، کائو که روی هم 90 درصد سرباره را تشکیل می دهند. 10 درصد بقیه عبارتند از: CaS، MnS، MnO، FeO و…
7. آهن را نیز به روش دیگری جدا می کنند و بیشتر آهن به دست آمده از کوره برای تهیه فولاد استفاده می شود.
فرآیند فعال سازی سنگ آهن و تبدیل آن به آهن خالص با واکنش های شیمیایی زیادی همراه است که به طور خلاصه برای تولید آهن باید واکنش زیر انجام شود.
(مراحل واکنش) Fe2O3→Fe3O4→IronO→آهن
3Fe2O3+CO↔2Fe3O4+CO2
Fe3O4+CO↔3 FeO + CO2
آهن + دی اکسید کربن↔آهن + دی اکسید کربن
نمودار شماتیک مراحل تولید آهن و فرآیندهای مختلف آن به شرح زیر است:
مراحل تولید آهن
مطالب مرتبط: جستجوی جداول استاندارد برای ورق فلز (آهنی و غیر آهنی)
مواد مذاب حاصله شامل سنگ آهن و سرباره است که به سمت بوش کوره که قسمت پایینی استوانه است جریان می یابد و به دلیل اختلاف وزن مخصوص آهن و سرباره از یکدیگر جدا شده و آهن می باشد. انتهای کوره توسط شیر تخلیه پایینی و سرباره توسط شیر تخلیه بالا تخلیه می شود.
آهنی که از کف کوره بلند استخراج می شود خالص نیست، بلکه به مقدار است و، از، ص، سی او نیز درون آن است.
در ایران به دلیل وجود معادن سنگ آهن فراوان از جمله معدن سینجان خاو در استان خراسان رضوی و معدن چاگرات در بافق یزد، کارخانه های ذوب آهن و تولید آهن و فولاد نیز رونق گرفت. ذوب آهن اصفهان و ذوب آهن مبارکه دو قطب مهم تولید آهن و فولاد در مرکز ایران هستند. آیا تا به حال فرآیند ذوب و عملیات کوره بلند در ذوب آهن را از نزدیک مشاهده کرده اید؟ چگونه می توان روند این فرها را بهبود بخشید؟ لطفا نظرات و پیشنهادات خود را در خصوص مراحل مختلف تولید آهن و فرآیندهای آن در انتهای این مقاله با ما در میان بگذارید.